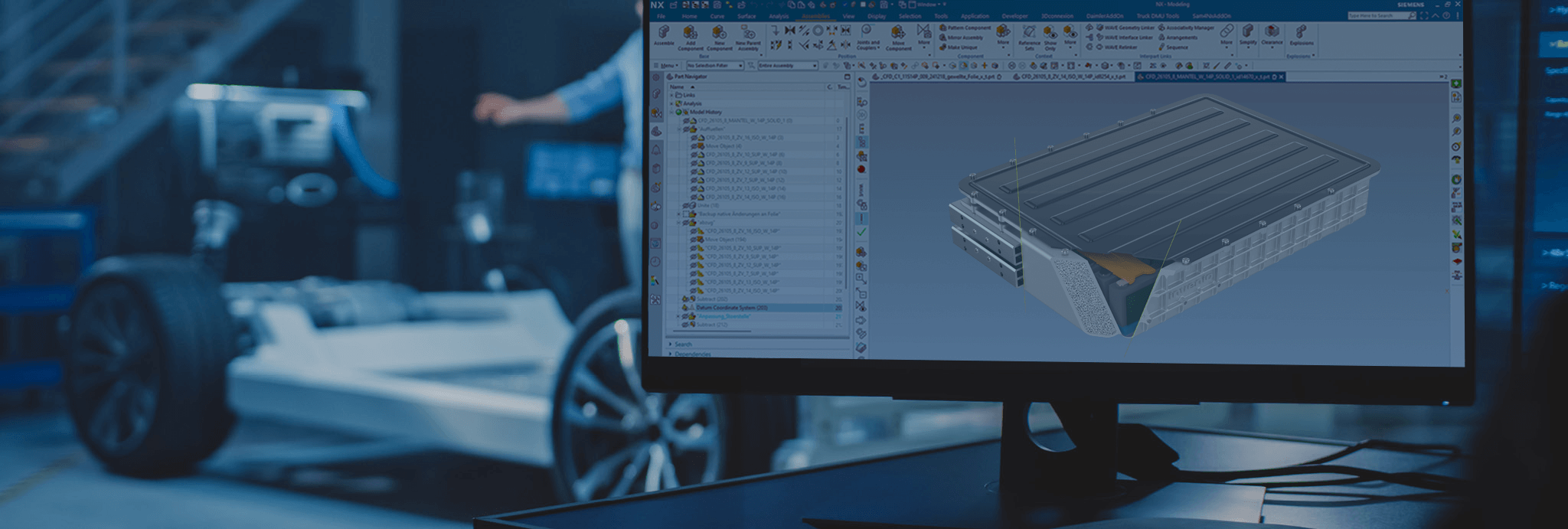
As an engineering service provider, invenio offers the holistic development of high-voltage batteries suitable for series production for BEVs and PHEVs. The scope of services can be realised in support of an existing development team or as outsourced system development for partial scopes. If required, on-site support is also possible.
Our services include:
Benchmarking and conception
Installation space analyses
Production-
orientated
design
Tolerances and
Drawings
Simulation (FEM, Crush, Crash, CFD)
Optimisation (weight and costs)
Testing and supplier
support
Production of
Subcomponents
Concept development includes analysis, goal description, application of concept methods, and evaluation. Through internal production locations for component scopes and partnerships with numerous suppliers, our developers can offer production-oriented development, drawing creation and supplier support
Our development scope includes the selection of the architecture and battery cell shape, their contacting and storage, as well as the connection of several modules - if modules still exist - and the control system to form an overall electrical system.
Depending on the concept, cooling plates or cooling lines can be integrated between the cells, modules or housings, or immersion cooling can be used for direct cooling. In a sealed housing, as a load-bearing or non-load-bearing structure of the vehicle, the energy storage system becomes a crash-relevant overall system.
We provide support in all development batches of high-voltage batteries up to series production and also with series production support.
Our expertise in the individual components:
Cooling plates
Immersion cooling
Contact
Expansion tank
Fastening
Special components with e.g. VDA or SAE coupling
Filling analyses and emptying
Volume determination and optimisation
Modular system for derivatives
Cast, extruded and deep-drawn components
Integrated cooling
Optimised for Crash and Crush
Weight-optimised
Consideration of EMC specifications
Sealing concepts
Assembly sequences
Cell contacting ZKS
Cell storage
Cooling the cells
Tolerance analysis
Assembly
Sealing
Bursting and venting
Creation of battery modules
Busbars (bent, twisted)
Cooling
Contact protection according to IP
Relay, sensor and contactor arrangement
Tolerance calculation
Holder
Plastic housing
Cable sets
Connection plates for LV and HV plugs
Rupture discs
Venting path
Sealing with solid and liquid seals
Design of O-rings
Measures for Crash and Crush
Holder made of sheet metal, cast iron and plastic
Weight optimisation
Holder for cooling, S-Box and cable sets
Benefit from our independent opinion, concept development, evaluation, selection and constructive implementation of components. We can take over the preparation of enquiry documents, as well as the implementation of the enquiry and evaluation for decision documents and the coordination of suppliers.
Manufacturing processes and example scopes for traction batteries:
Aluminium extrusion presses for e.g. housings, modules and crash topics
Sheet metal forming and stamped parts for e.g. housings, cell contacting systems (ZKS), holders and busbars
Plastic injection moulded parts for e.g. cooling lines, insulation components, connectors, housings and holders
Machining for e.g. contact pins, cast parts and spacer sleeves
Plastic tubes for e.g. cooling lines
Welding for e.g. cell contacts, housings and spacer sleeves
Sealing with e.g. liquid seals, moulded seals or O-rings
Aluminium die casting, gravity die casting and sand casting for e.g. holders, housings, connector interfaces and crash topics
Intelligent invenio software (VT-DMU) for checking derivatives, distances and assemblies
Short-term production of prototypes to secure your test set-up
Independent technically sound second opinion on one's own specialist are
Standard-compliant drawings and specifications for enquiries with suppliers
YOU WOULD LIKE TO CONTACT US?
We will be happy to answer any questions you may have!